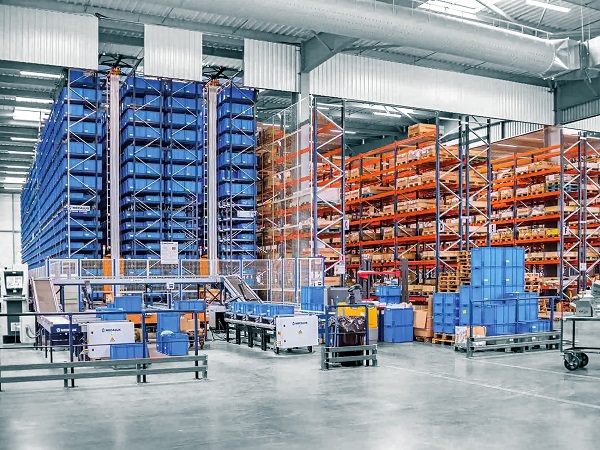
Automated Storage & Retrieval System (AS/RS)
Automated Storage & Retrieval System (AS/RS) – a flexible, high-density, high-speed and flexible automated cargo sorting, storage, storage and retrieval solution with up to a vertical storage space 40m.
The AS / RS automated warehouse is ideal for frozen warehouses, parts and equipment, semi-finished and finished products.
Contact us for advice on automated warehouse solutions, smart warehouses and automation solutions for smart factories, please contact:
VIETNAM CNC & TECHNOLOGY APPLICATION JOINT STOCK COMPANY
Hotline: 0915744664/0915740880
Email: Sales01@cncvina.com.vn / Sales03@cncvina.com.vn
Automatic pallet warehouse with automatic storage and retrieval system (AS / RS) is a smart warehouse solution widely used in beverage, frozen food, mechanical, and electrical industries, logistic, by the ability to store goods (which are pallets) make the most of the factory height (up to 40m) and easily retrieve inventory without the need for human appearance in the warehouse. The AS / RS automated warehouse is an important component of the smart factory that makes the production process automated, flexible, time-saving and efficient.
[toc heading_levels="1,2,3,4"]
Pallet storage systems feature high product storage density, high load capacity with high I / O operations and flexibility. In particular, it is safe for users to transport, carry heavy goods on high and export goods to the ground.
Automatic pallet storage system in the future will be the trend of choice for businesses because of its productivity and automation.
What is Automated Storage & Retrieval System (AS / RS)?
Automated Warehouse Pallet Storage and Retrieval System (AS / RS) -Also commonly known as ASRs warehouse is a warehouse automation solution specially designed to store and retrieve products and inventory on demand. . The AS / RS automated pallet warehouse ensures that materials are accurately stored and handled and can be found when needed, and manufacturers can reduce waste and improve performance right from their warehouse operations.
AS / RS technology changes dramatically over time. More and more warehouse management technologies, storage and export systems are more automated and safer. The supporting systems for the warehouse work include shuttle, rack, crane, lifting, conveyor, vertical lift module (VLM), small payload, unit load or others. It is usually integrated with warehouse execution software (WES), warehouse management software (WMS) or other control measures.
The term AS-RS stands for Automated Storage and Retrieval Systems, which means automatic storage and retrieval systems. The AS-RS storage racks include a rigid structural racking system combined with an automatic crane system for import and export. A special feature of AS-RS is the highly designed system, making the most of the warehouse height and lifting capacity of the crane.
If it is designed to add an automatic conveyor system, the AS-RS warehouse completely does not need human appearance to manipulate the warehouse. Automatic pallet warehouse is extremely suitable for cold storage, freezer, seafood, beer, and beverage. Logistic warehouse and storage of spare parts, equipment, inventory ...
Where the products are stored at deep negative temperatures, not safe for humans.
How does automatic pallet warehouse work?
The main structure of a pallet warehouse includes: The system of racks, shelves with a solid structure of many floors. Where goods (palletized products) can be stored in individual boxes. Each cell is assigned an ID that stores necessary information on the system, available or empty status is always updated in real time.
When the pallet is stocked, the system will manage all information related to that pallet through the identifier. The system automatically calculates and gives the storage location with the appropriate ID for the parcel, pallet based on the criteria of size, weight, sorting area (scripted before). The technology being applied popularly today is tracking pallet in warehouse using indoor positioning system & IoT, RTLS (Real-time Location Service).
At the same time, the warehouse management system also calculates the nearest path from the inlet to the storage location to save time and energy.
When exiting the warehouse, the system also self-identifies the pallet through this code and retrieves the goods quickly.
Of course, how fast or slow the delivery of goods depends on the size of the warehouse, the capabilities of handling systems and equipment, loading / unloading (cranes, industrial conveyors, shuttles, robots, fencing ...) But compared to traditional warehouse, this smart warehouse solution brings out remarkable efficiency.
These operations are based on intelligent operation and connection of roller conveyor, 90 degree curved conveyor, sorting sorting system, crane / lifting crane, shuttle feeder, industrial robot, barcode reading system ...
Not only does the export and import of goods optimize and automate, the AS / RS warehouse system also has the features to manage the shelf life of products and make notifications for managers , handling shipping plans.
Types of automated storage & retrieval systems (AS / RS)
The automatic storage and retrieval system (AS / RS) has two main types: Unit-Load AS / RS and Mini-Load AS / RS. Between these two main groups, there are six main types of AS / RS systems:
- AS / RS crane (Fixed aisles & movable aisles)
- Small load AS / RS cranes
- AS / RS based on Shuttle and Bot
- Conveyor-based AS / RS (Vertical, Horizontal and Robotic)
- Vertical lift module (VLM) AS / RS
- Micro load (Repository)
Automated storage and retrieval systems come in two main flavors: Unit-Load AS/RS and Mini-Load AS/RS. Within Mini-Load is a third subtype known as Goods-to-Person (G2P).
Unit-load automated storage and retrieval systems typically handle larger loads of goods and material (including weights measuring in thousands of pounds). Often, this means that the AS/RS tech is handling and moving full or partial pallets or cases. Unit-load AS/RS is a great option when pallet-level storage is limited and quick retrieval is critical.
Common types of unit-load AS/RS include fixed-aisle and movable-aisle unit-load cranes.
Compared to unit-load AS/RS, mini-load AS/RS typically handles smaller loads of product. Instead of full pallets, this often translates into a mini-load AS/RS handling totes, trays, or cartons. These systems are sometimes also called “case-handling” or “tote-stacking” systems. Mini-load AS/RS is especially well suited for operations that require storage locations for a large amount of SKUs but which lack the floor space required for traditional carton-flow shelving to provide a pick face for each SKU. Mini-load AS/RS systems can also be used to buffer and efficiently release/sequence product to picking or palletizing stations, and can be used to automatically replenish pick locations like carton-flow.
Common types of mini-load AS/RS include mini-load AS/RS cranes and shuttles carousel-based AS/RS, and Vertical Lift Modules.
Goods-to-Person (G2P) falls within mini-load AS/RS as a subtype best suited for split case order fulfillment. Though there are different types of G2P technology, the general principle remains the same: An automated storage system delivers SKUs to a stationary pick station, where the operator fills discrete orders.
AS / RS is based on a shuttle bus
AS / RS based on shuttle feeder shuttle: takes the pallet from the roller conveyor, the crane or the industrial robot arm then delivers the goods in / out. It can move forward and backward like a shuttle or a "bot" that runs on rails between a support structure. The feeder can rotate 90 degrees flexibly to help put the pallets in the storage cell position.
They can operate at one level or more, depending on the needs of the activity, and can be powered by batteries.
When an item is requested, the shuttle bus will move to the location of the product and pick up the carton / pallet containing the requested item. Then it goes directly to the conveyor,
Different shuttles use different designs to deliver different benefits. For example, a model is oriented vertically to optimize floor space. The feeder vehicle travels across the perimeter of the rack and then moves into an aisle to retrieve an item and transfer it to its integrated workstation.
One model uses a vertical stand, but each bot moves on the floor and climbs vertically to grab its items. It then goes downstairs and distributes the pallet to a remote workstation independently. It will queue at the workstation until it is selected and then automatically assigned a new task and it repeats the process.
AS / RS is based on a conveyor belt
A conveyor-based AS / RS system consists of cartons of product or inventory that rotate continuously along a line. When the operator requests a particular item, the system will automatically rotate to reach the right box so that the item can be selected. An integrated light will tell the selector which carousel, price, and item to choose.
The AS / RS is based on a conveyor belt that can consist of a horizontal conveyor (crates that move horizontally, like on a ferris wheel) or a vertical conveyor (crates move vertically). Horizontal conveyors are commonly used for small items and parts, as well as for materials or raw materials.
Factors to Consider Before Selecting an AS/RS Solution
If you are considering implementing automated storage and retrieval in your operation, it is worthwhile putting some thought to the considerations below, as these data points will prove pivotal in your discussions with a systems integrator or warehouse design consultant:
Throughput: How many hourly transaction/number of cycles are required by aisle?
Storage locations: What is the required capacity of the system? Is it single or double deep?
Product Specifications: What will be handled?
SKU Data: How much of each SKU will be stored? Based on its movement, should it be spread across multiple aisles of consolidated?
Order Profile: What is the order profile of the outbound work? Should SKU affinity be a consideration?
Weight: Some machines have a per tote capacity which is better suited to different product types.
Speed: Different machines have different down aisle speeds based upon the type of mast or shuttle, its mass, and maximum velocity.
Aisle length: Different machines will have a length of the aisle which is optimum for acceleration and deceleration and will provide the maximum dual cycle throughput in a hour
An automatic pallet warehouse AS / RS will help you maximize the usability and safety of the warehouse system, easily manage the storage and import of your goods. Smart modular warehouse, smart pallet warehouse with
Collaborative robot, Robotic Palletizing, Automatic guided vehicle-AGV with warehouse management software, loading / unloading system, industrial conveyor belt has been and will be important components. indispensable importance of smart factories in modern production.
Customers who have demand for smart warehouse solutions and automation solutions for smart factories please contact:
VIETNAM CNC & TECHNOLOGY APPLICATION JOINT STOCK COMPANY
Factory: Song Cung industrial site, Dong Thap commune, Dan Phuong district, City. Hanoi Vietnam
Phone: +84.915 74 4664 / +84.915 74 0880 Fax: +84.24.37805007
Website: www.cncvina.com.vn; www.maytudong.com.vn; www.cncvina.net
Email: Sales01@cncvina.com.vn / Sales03@cncvina.com.vn
OUR PARTNERS












