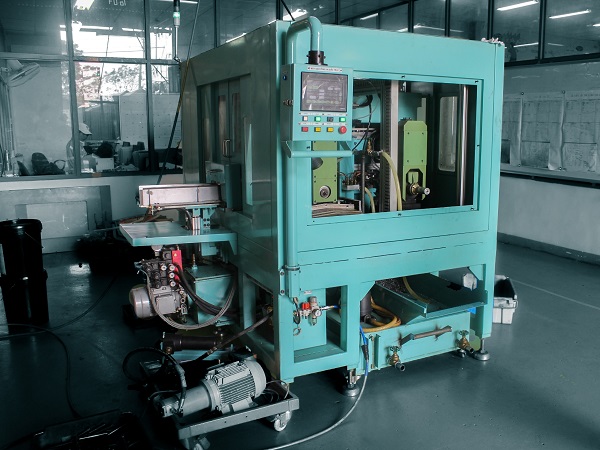
Integrated manufacturing machine
Application of Integrated manufacturing machine (dedicated 2-heads machining machine).
Machining incorporating drilling – tapping – chamfering – slotting is one of many specialized processing machines designed, manufactured and provided by CNCVina automation engineers to domestic and foreign customers. Automatic processing machine with 4 work-piece drill-taro lace-beveled edge-slotted is made according to individual requirements for each product of the customer.
Processing machines that incorporate facing milling, tapping and slotting machining with slides are the optimal solutions for production automation. Thanks to this 4-in-1 automatic machine, with only one installation, mechanical products can be machined 2 heads, slotted and taro with the required dimensions and tolerances.
Using integrated processing machines greatly reduces time compared to traditional machining methods. It often takes a lot of time and effort to check and fix the work-piece. The batch processing machine, integrated with automatic control has the advantage of processing mass products with very high productivity (about 2,000-2,500 products / shift). Time to finish 4 tasks (cycle time) in seconds.
Specifications of Model 171020816 integrated automatic processing machine
Reference size: 2000 (W) x 2500 (D) x 1800 (H) (mm).
Operation height of the machine: 915 mm from the floor.
3 phase source, AC 380 V, 50 Hz.
Control voltage: DC 24V
Air source requirement: 0.4 - 0.6 Mpa.
Hydraulic power requirement: Total maximum pressure 80 Mpa.
Big and small speed of detail: 1900 rpm, step forward 0.3mm / round.
Lace speed: 600 rpm.
Speed and parts slotting: 1900 rpm, step forward 0.3mm / round.
Machining program, cutting mode has been installed in the machine and easily changed. The machine can change the flexible settings according to each product model that customers provide before.
Structure and operation principle of integrated processing machine designed and manufactured by CNCVThe machine consists of 6 main clusters:
Lower frame frame, pedestal body and frame structure machine
Moving cluster (conveyor cluster)
The main axle cluster consists of 4 heads with facial function and taro and slit. Move with the guide rail slide. Automatic operation through servo control system and inverter.
Positioning, positioning and clamping clusters
Cold water container assembly
Hydraulic barrels
Parts are fed into the conveyor belt simultaneously and moved into the inner space of the four heads. To the machining position, parts are positioned and clamped tightly with JIG structure, clamping correctly. At the same time, the machine will perform the same task at the same time as both sides on both big and small heads on the part. Tapping holes and grooves. Then the finished product is taken out, ending cycle time.
Parts before and after processing with automatic integration machine
Features of the integrated processing machine
Mass machining with high productivity
Processing products have high dimensional stability
It is built according to the standard module that makes the machine long and easy to replace
Automation of transport between stages in the machining process
The chip is blown clean and brought out with cool slurry and chip conveyor
The product is issued continuously into the "Input" cluster and is moved to the default position 1 & n 2 to At the beginning of the product, it is then moved to the convenient location & to complete the product The product is finally removed in the "Output. The product is fed into the clamping position and processed automatically simultaneously by the spindle ends. The tasks that can be applied to integrated machining machines are: milling, turning, head face milling, drilling, boring, tapping, chamfering, grinding ...
Basic operation of the integrated processing machine
The integrated processing machine has two operating modes, Manual mode and Automatic operation mode (Auto). In manual mode, workers shift the main spindle milling, drilling, turning, tapping, to the desired locations. With automatic mode, the product is continuously supplied to the input assembly and moved to the machining position. After the product is positioned correctly by jig jig, the machining head enters the task. The processed product will be taken to the output (Automatic) cluster automatically for workers to take out.
Attention:
Running cycle:
- After the device has returned to its original state, the Return light is bright, then switch to Auto. Click simultaneously Reset and Stop to clear all product counters and timer to 0
- After switching to Auto, the Start light flashes (Start Lamp on HMI flashes but no effect for running Auto for safety reasons)
- Press the Start 1 and Start button at the same time. The 2 rotating tables will automatically rotate an angle of 900. At the first run This will only have active drilling clusters
- After the drill phrase is completed, 2 Start 1 and Start 2 lights will blink. Put the product in, At the same time, 2 Start 1 and Start buttons 2 rotary tables will automatically turn 1 corner 900. At this 2nd run Drill cluster and chamfer cluster operate.
- After 2 drilling and chamfering clusters are done, 2 Start 1 and Start 2 lights will blink. Set up the property Click on the Start 1 and Start buttons at the same time. 2. The turntable will automatically rotate at an angle of 900. At times run this 3rd all 3 drill-chamfer-doa clusters will work.
- After all 3 drill-chamfer-reams have completed the Start 1 and Start 2 lights will blink. Set up the property The product enters and presses 2 Start 1 and Start buttons at the same time If you run this, all 3 clusters will work.
- Every time you finish, when the Start 1 and Start 2 lights are blinking, you can press to execute new cycle.
Steps to change the model, DANDORY
Step 1. Switch the device to Manual mode
Step 2. Replace the positioning V block, change the distance of the conveyor to suit each model type
Step 3: Change the cutting tool
Step 4: Change the cutting mode
Step 5: Change the model on the monitor screen
Step 6: Run the machine manual mode In the process of running an integrated automatic machining machine, always follow the operating procedure given by the supplier of CNCVina.
Always clean the machine, check the electrical and hydraulic system before and after each shift. Maintenance, maintenance and periodic replacement for mechanical assemblies such as bearings, sliding rails, screw screws. Replace cutting oil, replace cutting tool after calculated product quantity. With the understanding and strict adherence to regulations during use. Any of your specialized machining machines will always ensure stable and long-term productivity and operation.
OUR PARTNERS












